Why Choose Us?
Rich Experience
"FANGRONG" brand established in 1998, we are the leader of straightening machine, drawing machine, and pointing machine in China.
Wide Range of Applications
We have rich experiences in aluminum industry, copper industry, stainless steel industry, titanium alloy industry, magnesium alloy industry, molybdenum alloy industry, lead alloy industry, set.
Reliable Product Quality
Our company has been providing customers with better quality products. Our business is always customer-oriented and focuses on creating customer service experience.
Excellent Customer Service
Our goal is to make professional first-class equipment, first-class service and first-class innovation, and realize product specialization, technology specialization, service specialization and teamwork.
What is Thread Rolling Machine?
A thread rolling machine is a specialized piece of industrial equipment used in the manufacturing process to create threads on cylindrical parts, such as screws, bolts, and studs. Instead of cutting threads into the workpiece (as done with threading dies or taps), a thread rolling machine forms threads through a cold-forming process. This process is often referred to as "thread rolling" or "thread forming."
High Production Efficiency
Speed: Thread rolling is a fast process, producing threads at a much higher rate compared to cutting or grinding methods.
Continuous Operation: Machines can run continuously with minimal downtime, making them ideal for high-volume production.
Superior Thread Quality
Strength and Durability: Rolled threads are stronger than cut threads because the grain flow of the material follows the thread contour, enhancing tensile strength and fatigue resistance.
Surface Finish: The rolling process produces a smoother surface finish with better wear resistance.
Material Savings
No Material Loss: Thread rolling displaces material rather than removing it, resulting in no material loss and better utilization of raw materials.
Efficiency: This material conservation translates to cost savings, especially in high-volume production.
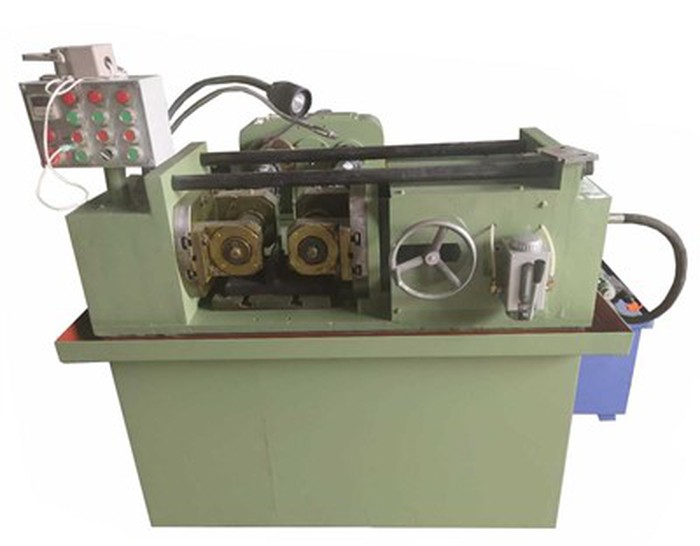
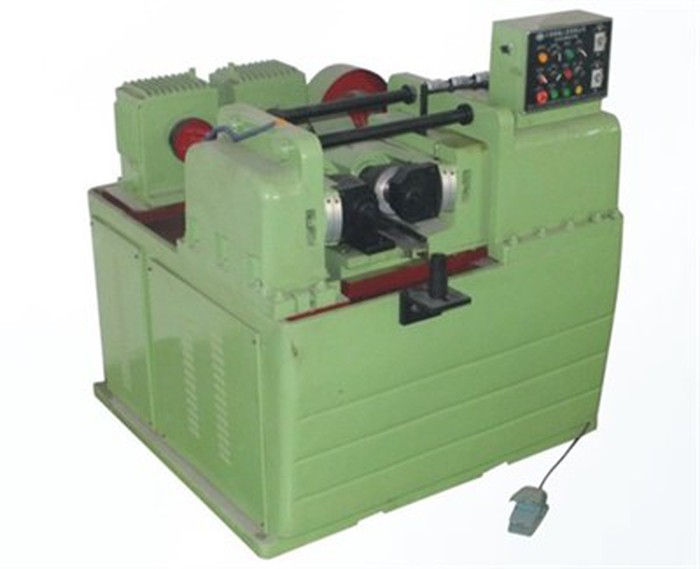
Versatility
Various Materials: Suitable for a wide range of materials, including ferrous and non-ferrous metals.
Different Thread Types: Capable of producing different thread forms, including metric, unified, Acme, and special profiles.
Consistency and Precision
Repeatability: The process offers high repeatability, ensuring consistent thread dimensions and quality across large batches.
Precision: Thread rolling machines can produce precise and uniform threads, meeting stringent tolerance requirements.
Mechanical Benefits
Increased Hardness: The cold working process increases the hardness and strength of the thread surface.
Reduced Stress Concentrations: Rolled threads have a more uniform stress distribution, reducing the risk of failure under load.
Environmental and Economic Benefits
Energy Efficiency: The process consumes less energy compared to thread cutting or grinding.
Lower Tool Wear: Rolling dies have a longer lifespan than cutting tools, reducing maintenance costs and downtime.
Types of Thread Rolling Machine
Flat die thread rolling machine
A flat die thread rolling machine has four main parts which include a conductor bar, pusher arm, and two flat dies where one is fixed and the other is moved backward and forward by a crank-type mechanism. The flat dies come with a thread profile machined into them and another thread profile inclined by the pitch of the thread they can create.
2-die cylindrical thread rolling machine
A 2-die cylindrical thread rolling machine has three variations which include infeed, thru-feed, and a combination of infeed & thru-feed. Infeed machines have two parallel dies that rotate in the same direction and at the same speed. One die is fixed while the other has lateral movements. The rolling process depends on friction to rotate the blank. In this case, the lateral movement is adjusted to set the thread pitch and diameter.
3-die cylindrical thread rolling machine
A 3-die cylindrical thread rolling machine comes in three variations. Two of the three dies are fixed while the third moves vertically or laterally based on the layout of the machine. The 3-die cylindrical thread rolling machine is selectively suited for long threaded items like lead screws.
Planetary thread rolling machine
A planetary thread rolling machine has the blanks fed into the dies like in a flat die thread rolling machine. The machine has two dies where the circular die rotates and the curved die is fixed. Some planetary thread rolling machines contain multiple curved segment dies mounted around the circular die. This feature ensures high production rates.
Application Of Thread Rolling Machine In Material Handling Equipment Manufacturing
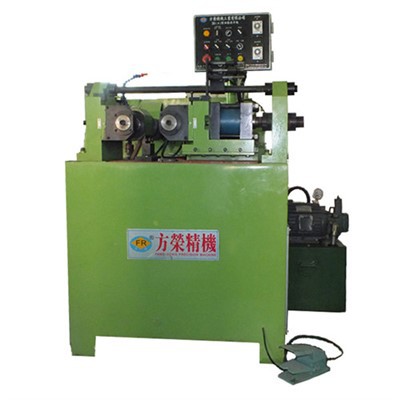
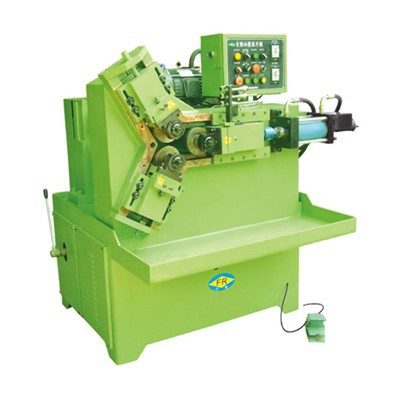
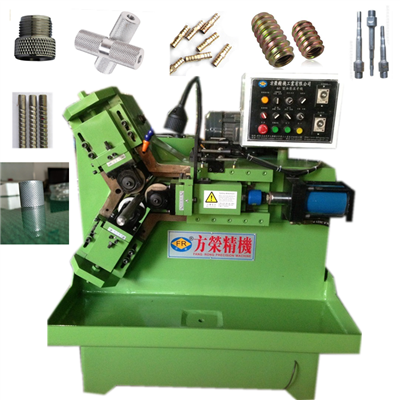
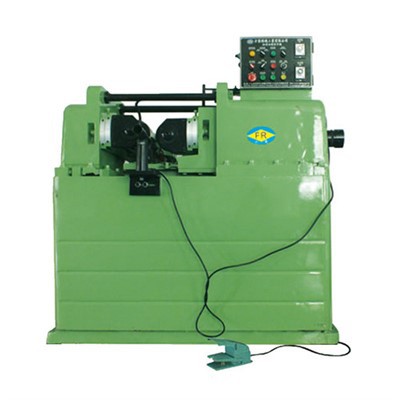
Conveyor Systems
Thread rolling machines are widely used to produce threaded components used in conveyor systems, such as threaded rollers, screws and fasteners. These components are critical in assembling and maintaining conveyor belt and roller systems used for material transportation.
Material Handlers and Trolleys
Threaded connections are critical in material handlers and trolleys, including threaded shafts, handles and fasteners. Thread rolling machines produce threads on these components to facilitate movement and handling of the material.
Lifting and Lifting Equipment
Threaded connections are used in lifting and lifting equipment such as threaded hooks, bolts and eyebolts. Thread rolling machines machine threads on these components to allow for secure connections and safe lifting of heavy objects.
Pallet handling systems
Pallet handling systems use threaded connections and include threaded pallet feet, corner brackets and fasteners. Thread rolling machines produce threads on these components for efficient, reliable pallet handling. Threaded connections are widely used in material handling racking systems, including threaded beams, columns and connectors. Thread rolling machines process threads on these components for assembly and adjustment of the frame structure.
Material handling lifts
Threaded connections are critical in material handling lifts, including threaded lift screws and adjustment bolts. Thread rolling machines produce threads on these components for a smooth and controlled lifting operation.
Material handling chutes and rails
Threaded connections are used in material handling chutes and rails, including bolts and rails that guide the flow of material. Thread rolling machines produce threads on these components for efficient material handling.
Material Handling Accessories
Threaded connections are critical in a variety of material handling accessories, such as threaded forks, clamps and extensions for forklifts and other handling equipment. Thread rolling machines are used to manufacture replacement parts and components for the repair and maintenance of material handling equipment. These machines ensure the availability of high-quality threaded parts for repairing material handling machinery.
Material Handling System Components
Threaded connections are widely used in various material handling system components to ensure the correct alignment and stability of material handling equipment.
Operating Logic of a Thread Rolling Machine
Workpiece Preparation
Initial Sizing: The workpiece, typically a cylindrical rod, is prepared to the required diameter slightly smaller than the final thread’s major diameter.
Material Suitability: Thread rolling is most effective on ductile materials like steel, aluminum, and brass, which can withstand the significant deformation without cracking.
Setup and Loading
Die Configuration: The machine is equipped with two or more dies, each with thread profiles. These dies can be flat, cylindrical, or planetary, depending on the machine type and application.
Workpiece Loading: The workpiece is fed into the machine either manually or through an automated feeding system.
Thread Rolling Process
Die Movement: The dies move in a linear or rotational manner to exert high pressure on the workpiece. This pressure causes plastic deformation of the material, creating the thread form.
Simultaneous Deformation: The dies simultaneously press against the workpiece, rolling it between them. This synchronized movement ensures the thread is formed uniformly around the workpiece.
Completion and Ejection
Thread Formation: As the workpiece moves through the dies, the thread profile is impressed onto it. The process is completed when the workpiece has passed through the entire length of the dies.
Ejection: The finished threaded workpiece is then ejected from the machine, ready for further processing or use.
The Considerations for Buying Thread Rolling Machine
Cost includes the initial purchasing price, the cost of accessories, and the equipment maintenance costs. On average, thread rolling machines are available at prices of about USD 5,000. The material being threaded and the demand of the production line determines the kind of thread rolling machine to be purchased. Buyers should consider their budget when investing in efficient thread rolling equipment. Furthermore, they should generally ensure a no scrap, lower tool cost, and lower labor formula to significantly reduce the costs.
The final quality of the rolled thread is dependent on the precision of the thread rolling machine. Apart from material choice, accuracy is determined by the preparation process of the blanks to be threaded. Conventionally, thread rolling displaces material, thus the diameter of the blank is generally smaller than that of the finished rolled thread’s diameter. In this case, the average precision can be achieved if the blanks are machined at tight tolerances of about 0.0005 inches. There is a further recommendation to include a 37-degree chamfer threaded at the end of each section to reduce the risk of chipping and an approximately 45-degree final chamfer.
The inclusion of cold working in thread rolling increases tensile strength by at least 30% more than cut threads. Rolled threads have an improved fatigue strength ranging from 50% to 75%. In this case, threads exhibit no loss of fatigue strength even if they are heated up to 500 degrees Fahrenheit. Some machines produce stronger threads that do not require expensive outside heat treatment. Generally, rolled threads are smoother and are damage-resistant when being handled.
The speed of thread rolling can go up to 200 feet per minute when working on materials like high-carbon steel and brass. However, buyers can obtain better results by employing slower speed. Thread rollers can achieve significant speed when the roller held in a holder is attached to the cross-slide while being presented radially or tangentially. The speed is slower if the roller is held on a swing stool. This is because of a lack of rigidity of the holder on the swing type.
It is vital to select a suitable material to enhance the accuracy and quality of the threads produced. Generally, if the material is hard, it becomes equally hard to be rolled, which might affect the service life of the dies. Also, as buyers purchase thread rolling machines, they should note that hollow profiles result in blank ovals due to the forces involved. On average, a suitable material should have a minimum elongation of 12%, a maximum hardness of about 40 HRC, and a maximum tensile strength of 1079 MPa. Furthermore, to improve the dies’ durability, some have coatings like CVD and PVD.
Working Principle of Thread Rolling Machine
Workpiece preparation
The process starts with a cylindrical workpiece made of materials such as steel, aluminum or other metals. The diameter of the workpiece is slightly larger than the desired finished thread diameter.
Feed the workpiece
The workpiece is fed between the two dies of the thread rolling machine. One of the dies is fixed while the other is movable and applies force to the workpiece.
Pressure and rolling
High pressure is applied to the workpiece while the movable die is rotating. This pressure causes the material to deform plastically and take on the shape of the threaded die. The fixed die has a thread profile and the workpiece is shaped to match this profile.
Radial displacement
When pressure is applied by the die, the material is displaced radially, creating threads. The pitch, depth and profile of the thread are determined by the shape and size of the die.
No material removal
Unlike cutting or grinding processes, thread rolling does not remove any material from the workpiece. Instead, it displaces and reshapes the material to form the thread, increasing efficiency and producing a stronger thread.
Thread geometry control
The thread rolling process precisely controls the size and geometry of threads, ensuring high precision and consistency.
Multi-pass thread processing
For some applications, threads may require multiple rollings to achieve the desired depth and strength. The workpiece is gradually rotated and passed through the die until the threads are fully formed.
Finishing and inspection
After thread rolling, the finished workpiece may undergo further finishing processes such as cleaning, heat treatment or surface coating. Additionally, the threads are inspected to ensure they meet the required specifications.
● When installing the thread rolling machine, make sure its grounding is reliable. The thread rolling machine manufacturer recommends that an appropriate fuse device be installed in the lead-in power supply. In order to make the operator more secure during use, it is preferable to install the leakage protection device. In addition, it is recommended to introduce a power cord to be buried in the installation.
● Turn on the electrical box equipment and carefully check if all the terminals inside are loose. If you find the problem, tighten them immediately. The thread rolling machine manufacturer reminds you that you need to check the status of the wires to ensure that the wires are complete and there will be no problem of broken skin. When problems are found, they should be replaced in time.
● During the test run after the power is turned on, it is necessary to pay attention to the operation of the hydraulic motor, and ensure that it is in a clockwise rotation state. In addition, the cooling water pump is also a very important component. If the coolant is reversed, the coolant will not come out, or it will come out very little. The main motor can be disregarded. It is determined according to the workpiece and the selection switch of the rolling mold used on the panel to rotate to the left or to the right. If the phase sequence is wrong, just leave the power cord free. It is ok to change the position of the two phase lines.
Troubleshooting of Common Thread Rolling Machine Problems
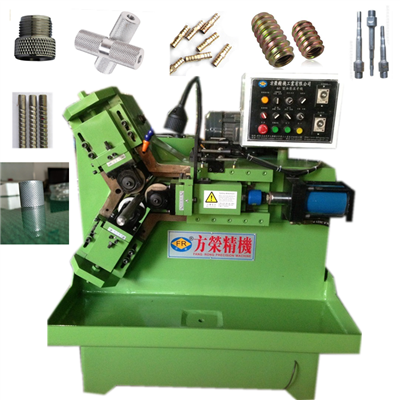
Misaligned Dies
Misaligned dies can lead to poor thread quality and increased wear on the machine. To troubleshoot, first, check the alignment of the dies according to the manufacturer’s specifications. Use precision measuring tools to ensure that the dies are parallel and correctly positioned relative to each other. Regularly rechecking and adjusting the alignment can prevent this issue from recurring and ensure high-quality threading.
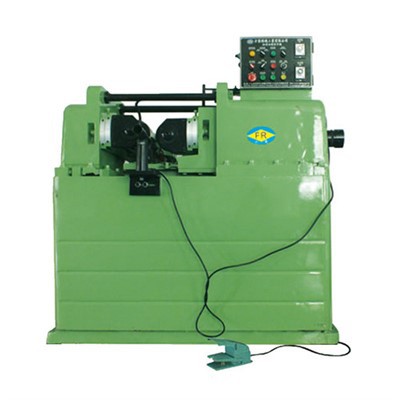
Inconsistent Thread Quality
Inconsistent thread quality can be caused by incorrect machine settings, worn-out dies, or improper material feed. Start by examining the dies for wear and replace them if necessary. Next, review and adjust the machine settings such as feed rate, pressure, and temperature to match the material’s requirements. Ensuring consistent material quality and correct machine setup can dramatically improve thread consistency.
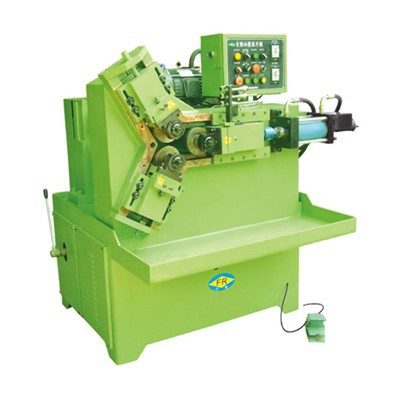
Operational Overloads
Operating the machine beyond its capacity can lead to frequent breakdowns and reduced lifespan. If signs of overload, such as excessive noise, vibration, or heat, are present, immediately reduce the load to within recommended limits. Check the machine’s operational manual for maximum capacity guidelines and adjust your production schedule accordingly.
8 Strategies for Thread Rolling Machine Efficiency
Optimal Machine Setup for Enhanced Performance
To begin with, achieving the peak of productivity in thread rolling operations depends on the machine setup. An optimal setup not only enhances performance but also ensures consistent quality in output.
Mastering Machine Parameter Adjustments
Another strategy in maximizing the productivity of your thread rolling machine lies in mastering its parameter adjustments. Fine-tuning these settings can lead to significant improvements in efficiency and product quality.
Routine Maintenance for Consistent Output
The next strategy to ensure your thread rolling machine maintains high productivity levels is through routine maintenance. Regular checks and servicing can prevent unexpected downtimes and maintain consistent output quality.
Troubleshooting Common Issues
The next strategy to maximize the productivity of your thread rolling machine involves adept troubleshooting of common issues. Quick identification and resolution of these problems are essential for reducing downtime and maintaining efficient operations.
Leveraging Advanced Techniques and Innovations
Embracing advanced techniques and the latest innovations is crucial for staying ahead in the competitive landscape of thread rolling.
Maximizing Operator Skill and Safety
Ensuring the skill and safety of operators is key to maximizing the productivity and efficiency of thread rolling machines. A well-trained operator not only enhances machine performance but also minimizes the risk of accidents.
Efficient Workflow and Process Optimization
Optimizing the workflow and processes around thread rolling machines is critical for achieving maximum productivity and efficiency. Streamlining operations can significantly reduce downtime and increase output quality.
Keeping Up with Industry Trends
Staying informed about the latest industry trends is vital for ensuring that your thread rolling operations remain competitive and efficient. Adapting to new technologies and methodologies can significantly enhance productivity and quality.
Our Factory
Dongguan Fangrong Precision Machinery Industry Co., Ltd., established in 1999, is a professional manufacturer of wire drawing machines, straightening machines, wire rolling machines and other equipment. The company is a professional manufacturer integrating development, production and sales, Our goal is to make professional first-class equipment, first-class service and first-class innovation, and realize product specialization, technology specialization, service specialization and teamwork.
Ultimate FAQ Guide to Thread Rolling Machine
We're well-known as one of the leading thread rolling machine manufacturers and suppliers in China. Please rest assured to buy discount thread rolling machine for sale here and get quotation from our factory. For customized service, contact us now.
thread rolling equipment, roll thread machine, thread rolling attachment for cnc lathe